Результаты испытаний на абразивную износостойкость по корунду, когда основным механизмом изнашивания всех исследуемых сталей является микрорезание, показали, что износостойкость линейно возрастает при увеличении содержания углерода в мартенсите до 0,9%.
При испытании по более мягкому абразиву – кремню пропорциональная зависимость износостойкости от концентрации углерода характерна только для низко- и среднеуглеродистого (до 0,5% С) мартенсита.
Отсутствие строгой пропорциональной зависимости между твердостью и абразивной износостойкостью
углеродистого мартенсита обусловлено увеличением способности мартенсита к деформационному упрочнению при повышении содержания в нем углерода более 0,5% вследствие активизации в высокоуглеродистом мартенсите при изнашивании процессов деформационного динамического старения.
Сущность деформационного динамического старения мартенсита состоит в том, что возникающие при пластической деформации дислокации активно взаимодействуют с атомами углерода, находящимися в октаэдрических порах кристаллической решетки мартенсита. В результате этого взаимодействия атомы
углерода перемещаются к дислокациям, образуя сегрегации. Высокая энергия взаимодействия дислокаций с сегрегациями из атомов углерода обусловливает сильное закрепление дислокаций и, соответственно, интенсивное деформационное упрочнение мартенсита.
Проведенный в ходе исследования рентгеноструктурный анализ поверхностей углеродистых сталей, как в исходном состоянии, так и после изнашивания в различных условиях показал, что абразивное воздействие приводит к резкому уменьшению ширины линии мартенсита. У высокоуглеродистых сталей при абразивном воздействии наблюдается исчезновение дублета линии.
Результаты испытаний при фрикционном воздействии твердосплавным индентором в безокислительной среде азота (при 20 и –196°С) и на воздухе показали, что рост концентрации углерода в сталях до 0,83% массы вызывает повышение износостойкости (снижение потери веса) при трении скольжения. Это связано с увеличением прочности мартенситной структуры, обусловливающим смену основного механизма изнашивания – от адгезионного к полидеформационному. Дальнейший рост содержания углерода в сталях до 1,35% массы сопровождается некоторым снижением износостойкости (увеличением потери веса) вследствие повышения хрупкости мартенситной структуры.
Уменьшение температуры испытаний в азоте от комнатной до –196°С вызывает ускоренный износ закаленных и низкоотпущенных высокоуглеродистых сталей, инициированный их низкотемпературным охрупчиванием, и, напротив, приводит к снижению интенсивности адгезионного изнашивания менее прочной стали 35 вследствие ее низкотемпературного упрочнения.
При трении на воздухе интенсивность изнашивания стали 35 резко снижается по сравнению с трением в безокислительной среде азота, поскольку образующиеся при фрикционном воздействии на воздухе окислы препятствуют адгезионному взаимодействию контактирующих металлических поверхностей. С другой стороны, фрикционное окисление приводит к охрупчиванию и, соответственно, снижению сопротивления усталостному изнашиванию поверхности высокоуглеродистых сталей. Охрупчивание деформированного поверхностного слоя сталей в результате его взаимодействия с кислородом связано с образованием хрупких пересыщенных твердых растворов кислорода в железе, а также с формированием преимущественно по границам растущих микротрещин окислов, способствующих ускоренному развитию трещин. Отпуск при 200ºC приводит к уменьшению сопротивления закаленных углеродистых сталей изнашиванию.
Анализ трибологических свойств и деформационного упрочнения при фрикционном нагружении твердосплавным индентором закаленных и отпущенных при 200°С углеродистых сталей показал, что микротвердость поверхностей изнашивания углеродистых сталей при трении скольжения с большими
контактными нагрузками возрастает по мере увеличения содержания углерода от ∼10 ГПа у стали 35 до 12,0–12,5 ГПа у сталей У8, У10 и У13.
Одним из методов защиты поверхности изделий из стали является гальванотехника, которая представляет собой электрохимический метод нанесения на них металлических и химических покрытий для придания им определенных свойств: защитных антикоррозийных, защитно-декоративных, декоративных, а также специальных: антифрикционных, для придания твердости, износостойкости.
Оцинкование, которое возможно как в барабанных вращательных установках, так и на подвесках разными методами. Метод горячего оцинкования – это самый прогрессивный, надежный, высокоэффективный способ защиты от различных видов коррозии. Оцинковка в виде оболочки является защитным барьером, сводящим до минимума действие окружающей среды, а также устойчивым на механические воздействия. Оцинкование также обеспечивает электрохимическую защиту, так как при соприкосновении со сталью создает гальванический элемент.
Хромирование, одно из самых нужных покрытий, относится к наиболее трудоемким процессам гальванотехники. Хромирование – электролитическое нанесение покрытия из хрома на поверхность металлического изделия для предотвращения коррозии, повышения сопротивления механическому износу и придания декоративного вида.
Никелирование, нанесение на поверхность изделий никелевого покрытия толщиной, как правило, от 1÷2 до 40÷50 мкм. Никелированию подвергаются преимущественно изделия из стали и сплавов. Никелирование применяется для защиты изделий от коррозии (в атмосферных условиях, в растворах щёлочей, солей и слабых органических кислот), повышения износостойкости деталей, а также в защитно-декоративных целях.
Однако физико-механические свойства изделий с толстым слоем покрытия изменяются, и при различных механических операциях (гибка, вальцовка и др.), производимых с ними, покрытие скалывается с их поверхности в виде отдельных чешуек и пыли, что снижает их срок службы и ухудшает условия эксплуатации в рабочей зоне.
Какова износостойкость материала на поверхности углеродистой стали? Возможно ли в дальнейшем применять к стали с нанесенной пленкой механические воздействия: изгиб, кручение?
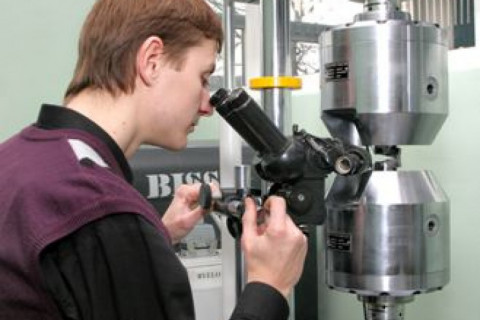
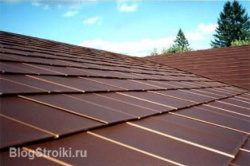